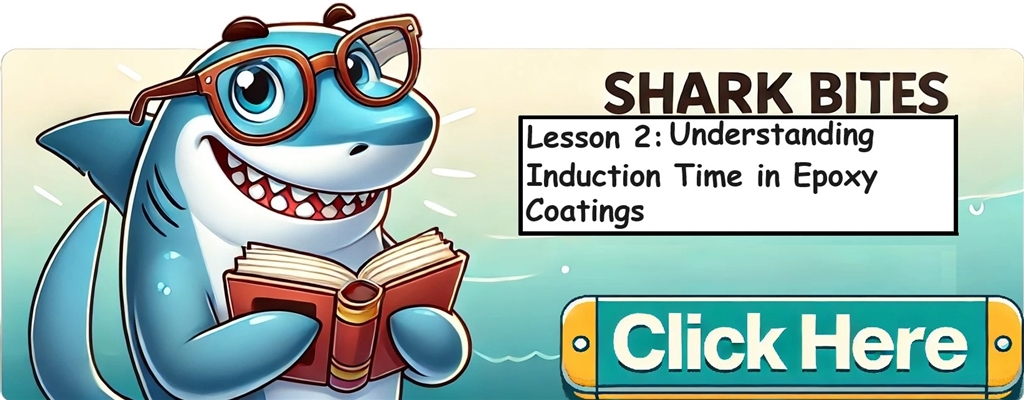
Understanding Induction Time in Epoxy Coatings:
A Crucial Step for Bathtub, Tile, and Countertop Refinishers In the bathtub, tile, and countertop refinishing industry, epoxy coatings are widely recognized for their excellent adhesion qualities and durability.
However, a critical yet often overlooked aspect of using epoxy coatings, particularly those with amine and polyamide resins, is the induction time.
Also known colloquially as “sweat-in” or “let it cook,” induction time is essential for ensuring the performance and longevity of the coating. This article will delve into what induction time is, its importance, and the detrimental effects of not allowing epoxies to properly induct.
What is Induction Time?
Induction time is the period required after mixing the epoxy resin and hardener during which the mixture must sit undisturbed to allow the chemical reactions to initiate and reach a homogeneous state.
This process is vital for the components to start reacting and forming the necessary bonds that will result in a robust and durable coating.
To put it simply, induction time means to “mix and let sit.”
Why is Induction Time Important?
1. Chemical Reactions: Epoxy resins and hardeners undergo a series of chemical reactions once mixed. Induction time ensures these reactions commence properly, allowing the mixture to achieve the correct viscosity and consistency.
2. Homogeneity: Proper induction time allows the components to mix thoroughly, ensuring a uniform distribution of the hardener throughout the resin. This homogeneity is crucial for the coating’s performance.
3. Adhesion: One of the primary benefits of epoxy coatings is their strong adhesion. Induction time helps optimize the adhesive properties of the coating, ensuring it bonds effectively to the substrate.
4. Curing: The curing process of epoxy coatings is highly dependent on the initial chemical reactions that occur during induction. Proper induction time sets the stage for a consistent and thorough cure, leading to a more durable and resilient finish.
Detriments of Skipping Induction Time Failing to allow epoxy coatings to properly induct can significantly impact their performance, potentially reducing their effectiveness by
up to 50%!.
Here are some specific detriments:
1. Poor Adhesion: Without proper induction, the epoxy may not adhere well to the surface, leading to peeling, chipping, and flaking. This is particularly problematic in high-wear areas like bathtubs and countertops.
2. Incomplete Curing: Skipping induction time can result in incomplete curing, leaving the coating soft, tacky, and prone to damage. This compromises the durability and protective qualities of the coating.
3. Weak Chemical Resistance: Epoxies are known for their resistance to chemicals and moisture. Improper induction can diminish this resistance, making the surface more susceptible to staining, etching, and other forms of chemical damage.
4. Inconsistent Finish: An uneven or inconsistent finish can result from inadequate induction, leading to aesthetic issues such as blotches, streaks, and an uneven gloss.
Practical Example:
Shark Grip Coatings Polyamide Resin To illustrate the importance of induction time, let’s look at a specific example using Shark Grip Coatings Polyamide Resin, known for its excellent performance in immersion service.
1. Mixing Ratio: The mix consists of equal parts - 1 part A resin and 1 part B activator.
2. Vigorous Mixing: These two parts must be mixed vigorously to ensure thorough blending.
3. Induction Period: After mixing, the blend must sit for 30 minutes to properly induct. This step is crucial for the chemical reactions to start and the mixture to become homogeneous.
4. Thinner Addition: Only after the induction period should the proper thinner be added for spray application. It’s important not to add the thinner during the induction mix as this will xxxx the process.
Thinner is used to adjust the viscosity for spraying, and the amount needed can only be gauged accurately based on the viscosity after induction, not from the total mix.
We’ve used Shark Grip Polyamide Epoxy resin as an example, but it’s important to note that induction is required for almost all solvent-based epoxy resins that are not 100% solids.
Conclusion: Induction time is a critical step in the application of epoxy coatings in the bathtub, tile, and countertop refinishing industry. Understanding and respecting this period ensures that the coatings achieve their full potential in terms of adhesion, durability, and overall performance. We at EAH Industrial are educating re-finishers on the importance of induction time, so they can enhance the quality and longevity of refinishing projects, leading to greater customer satisfaction and fewer call backs.
Remember, letting the epoxy “sweat-in” or “cook” is not just a recommendation it's a necessity for achieving optimal results.
By: Gary A. Goel
Founder : Shark Grip Coatings.
By
Excellent information, thanks! I'm assuming the sweat-in procedures are the same for Liquid Porcelain Enamel (LPE)?
Add New Comment